The Rise of Electric Moulding Machines in Metal Fabrication
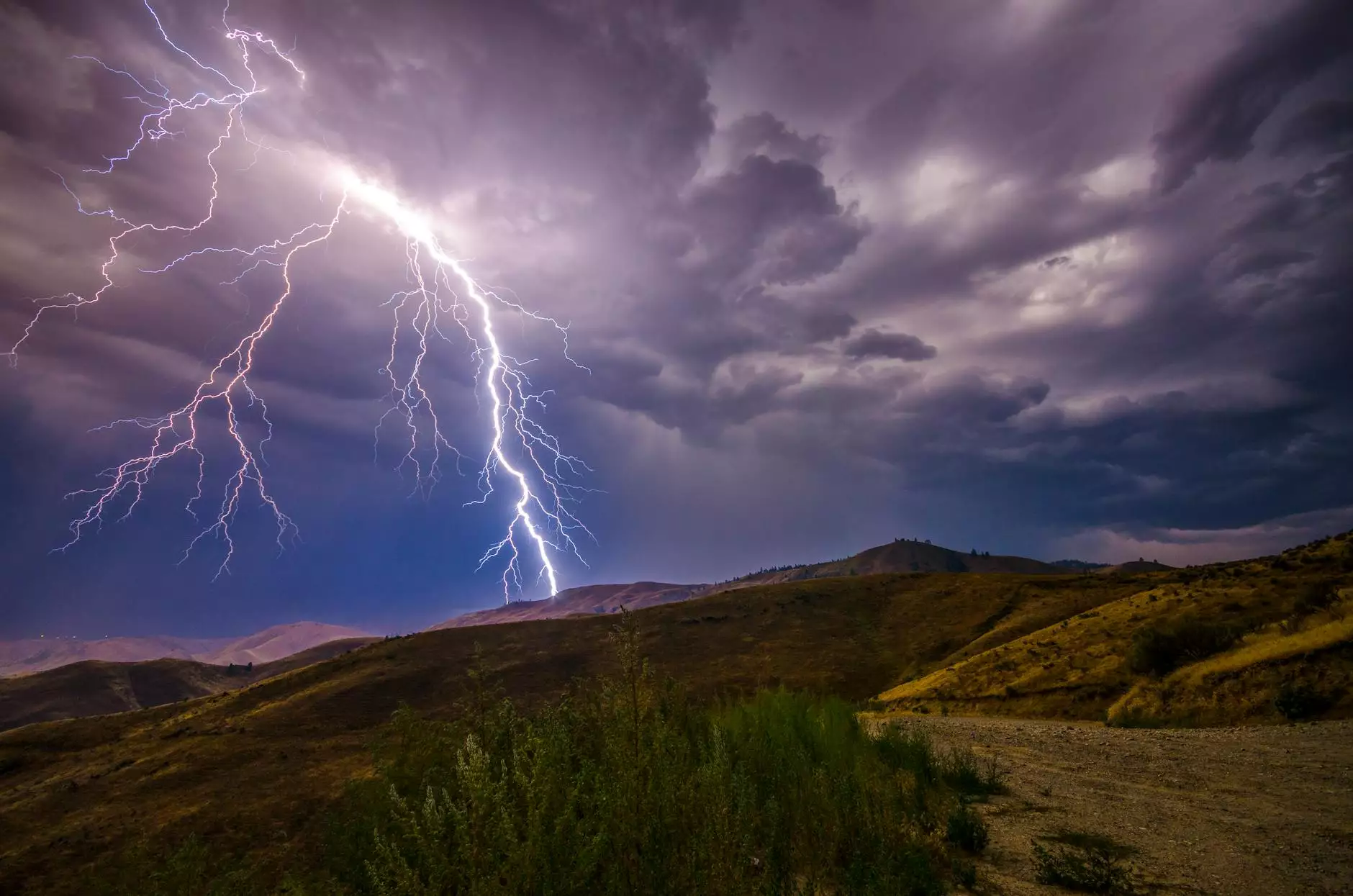
In the ever-evolving landscape of manufacturing, the adoption of electric moulding machines has emerged as a transformative trend, especially within the realm of metal fabrication. These sophisticated machines not only streamline production processes but also introduce several benefits that improve overall product quality and operational efficiency.
Understanding Electric Moulding Machines
Electric moulding machines are designed to perform various tasks related to the shaping and forming of materials, primarily metals. Utilizing electric drives instead of traditional hydraulic systems, these machines offer remarkable precision and enhanced control over the moulding process. This modern approach results in significant advantages, including decreased energy consumption, reduced operating costs, and improved product consistency.
Key Advantages of Electric Moulding Machines
- Energy Efficiency: One of the most notable benefits of electric moulding machines is their energy efficiency. Unlike hydraulic machines that consume a considerable amount of power, electric moulding machines are designed to use energy more sparingly. This efficiency translates into lowered operational expenses, making them a cost-effective option for metal fabricators.
- Reduced Maintenance: Electric systems typically require less maintenance compared to their hydraulic counterparts. With fewer moving parts and less hydraulic fluid to manage, maintenance becomes convenient and less frequent, allowing businesses to focus on production rather than repairs.
- Enhanced Precision: Due to their advanced engineering, electric moulding machines offer higher precision in the manufacturing process. This capability results in fewer defects and a reduced need for rework, which ultimately improves productivity and profit margins.
- Eco-Friendly Technology: The shift towards electric systems aligns with global trends towards sustainability. Electric moulding machines produce fewer emissions and reduce the risk of hydraulic fluid leaks, contributing to a cleaner working environment.
- Improved Safety Features: Modern electric moulding machines are equipped with advanced safety features, including emergency stops, overload protection, and enhanced guarding systems. These features ensure a safer work environment for operators and significantly reduce the risk of accidents.
Applications of Electric Moulding Machines in Metal Fabricators
The versatility of electric moulding machines makes them suitable for various applications in metal fabrication. Some common uses include:
- Injection Moulding: Electric moulding machines excel in injection moulding processes, catering to the production of intricate metal components where precision is paramount.
- Blow Moulding: These machines are also used in blow moulding applications, efficiently creating hollow parts for industries like automotive and consumer products.
- Thermoforming: Electric moulding machines facilitate thermoforming, making it possible to shape and mold materials with minimal waste and maximum accuracy.
Market Trends and Innovations
The demand for electric moulding machines continues to grow, driven by innovations in technology and the pursuit of greater operational efficiency. Notable market trends include:
1. Automation and Smart Manufacturing
As the industry shifts towards smart manufacturing, electric moulding machines are increasingly incorporated into automated systems. This evolution allows for sophisticated data collection and machine learning, enabling manufacturers to optimize processes in real-time and predict maintenance needs more effectively, thereby minimizing downtime.
2. Integration with Industry 4.0
The Industry 4.0 revolution has brought significant changes to how manufacturers operate, and electric moulding machines are at the forefront of this transformation. By integrating with the Internet of Things (IoT), these machines can communicate with other devices in the production line, leading to enhanced monitoring, data-driven decision-making, and greater operational synergy.
3. Customization Potential
Manufacturers are increasingly demanding customized solutions. Electric moulding machines can be tailored to meet specific production requirements, offering flexibility that is paramount in today’s competitive market. This customization can lead to innovations in design and functionality, ultimately satisfying diverse customer needs.
Challenges in Adopting Electric Moulding Machines
Despite their numerous advantages, transitioning to electric moulding machines can pose challenges for metal fabricators. Factors such as initial investment costs, the need for employee training, and industry resistance to change can slow down adoption. However, these challenges can be effectively managed:
- Comprehensive Training Programs: Investing in skilled operators through training can enhance the effectiveness and efficiency of new electric moulding systems.
- Assessing Long-Term ROI: Metal fabricators should evaluate the long-term return on investment (ROI) of electric moulding machines, considering not just initial costs but also the reduction in energy consumption and maintenance expenses.
- Transition Strategies: Implementing a phased transition approach can help mitigate disruptions to production. Gradually integrating electric machines can allow fabricators to adapt without sacrificing output.
Conclusion: Embracing the Future of Metal Fabrication
The adoption of electric moulding machines represents a significant step forward for the metal fabrication industry. With their energy efficiency, precision, and automation capabilities, these machines not only meet contemporary manufacturing demands but set the stage for future innovations. By embracing this technology, companies position themselves competitively and pave the way for sustainable growth.
As industries continue to evolve, the successful integration of electric moulding machines into manufacturing processes will likely dictate the leaders of tomorrow. Metal fabricators must remain vigilant, adaptable, and willing to invest in the technological advancements that will drive their success in an increasingly competitive market.
For more information on electric moulding machines and how they can revolutionize your manufacturing processes, visit deepmould.net.