Understanding Plastics Injection Molding
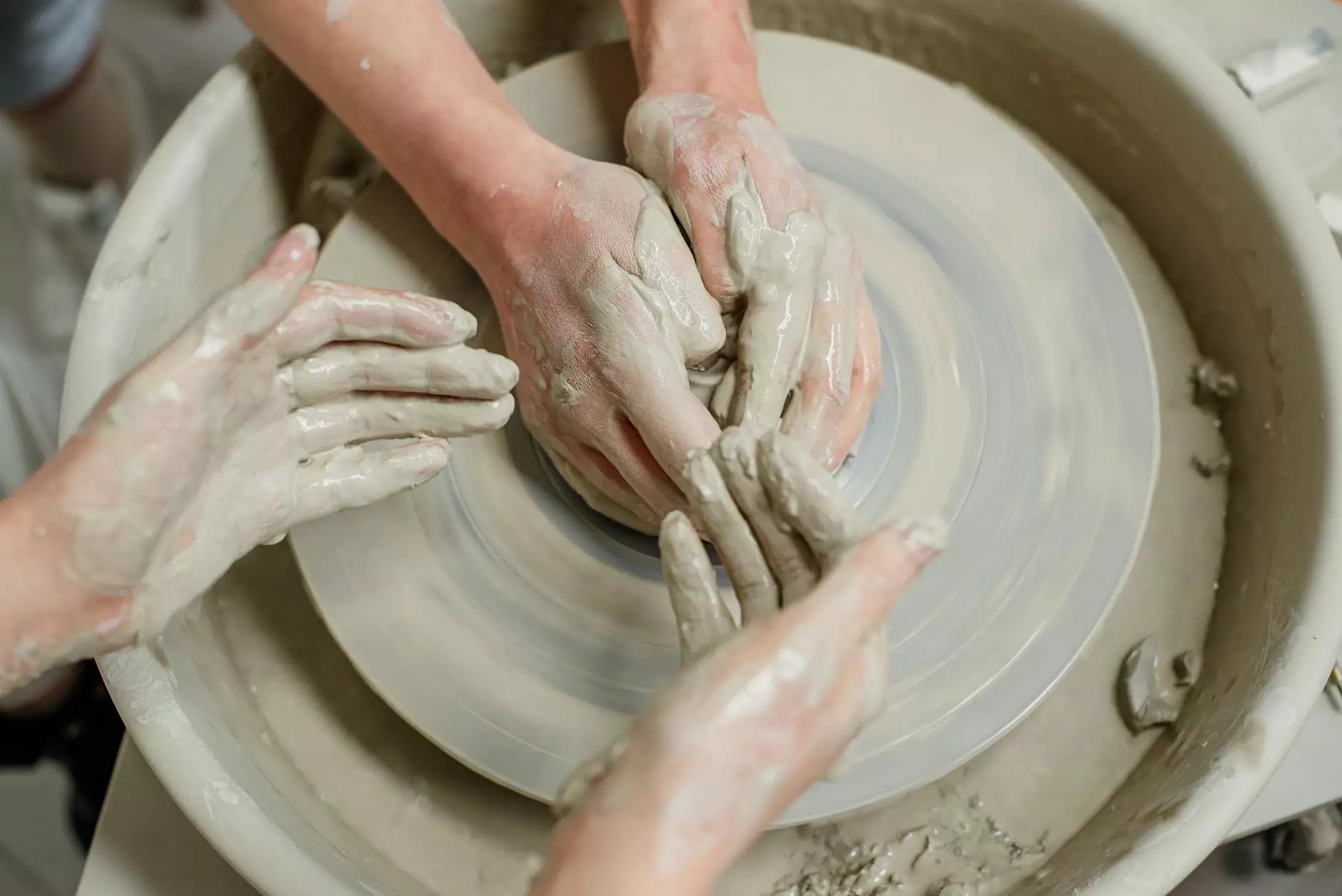
Plastics injection molding is a revolutionary manufacturing process that has transformed the production of plastic products. This method allows for the mass production of intricate parts with exceptional speed and precision. As industries continue to evolve, understanding the intricacies of this process becomes paramount for manufacturers looking to innovate and maintain competitive advantages.
The Basics of Plastics Injection Molding
At its core, plastics injection molding involves injecting molten plastic into a mold to create a specific shape. The process can be broken down into several key steps:
- Melting: Plastic pellets are heated until they become a molten substance.
- Injection: The molten plastic is injected into a mold under high pressure.
- Cooling: The plastic cools and solidifies in the mold.
- Demolding: Once cooled, the finished part is removed from the mold.
Why Choose Plastics Injection Molding?
The choice to utilize plastics injection molding in manufacturing comes with several significant advantages:
- High Efficiency: This process allows for quick production cycles, making it ideal for large-scale manufacturing.
- Complex Designs: Injection molding can create intricate shapes that are often impossible to achieve with other manufacturing techniques.
- Material Variety: A wide range of plastic materials can be used, allowing for versatility in product design.
- Cost-Effectiveness: Once the initial mold is created, the cost per unit decreases significantly in mass production.
Applications of Plastics Injection Molding
The versatility of plastics injection molding means it is widely used across various industries. Some notable applications include:
- Automotive: Components like dashboards, bumpers, and various intricate parts.
- Consumer Products: Everything from toys to home appliances is manufactured using this method.
- Medical Devices: Injection molding is crucial in producing precise parts for medical instruments and devices.
- Electronics: Housing for electronic circuits, connectors, and many other components.
The Role of Deep Mould in the Injection Molding Industry
As a leader in the field, Deep Mould has established itself as a go-to provider for high-quality injection molded components. The company is dedicated to innovation in the area of plastics injection molding and consistently collaborates with clients to meet their unique needs.
Expertise and Innovation
Deep Mould prides itself on leveraging cutting-edge technology and years of expertise to produce molds that stand the test of time. The team recognizes the distinct requirements of different sectors, especially metal fabricators, ensuring that each project is tailored to meet specific criteria.
Customer-Centric Approach
Every project at Deep Mould begins with a thorough consultation to understand the client’s requirements. The solutions provided are based on a blend of technical proficiency and customer feedback, leading to optimal results in the plastics injection molding process.
Challenges in Plastics Injection Molding
Despite its numerous advantages, plastics injection molding does come with its own set of challenges, which manufacturers must navigate:
- Initial Costs: The upfront investment in mold creation can be substantial, although costs decrease with mass production.
- Material Limitations: Some materials may not flow well in the mold or may not be suitable for certain applications.
- Technical Complexity: The process requires skilled professionals to handle machinery and troubleshoot issues that arise.
The Future of Plastics Injection Molding
As technology continues to advance, the future of plastics injection molding holds exciting possibilities. Innovations could include:
- 3D Printing Integration: Merging traditional injection molding techniques with 3D printing for quicker iterations.
- Eco-friendly Materials: Development of biodegradable plastics to reduce environmental impact.
- IoT and Smart Manufacturing: Implementing smart technologies for enhanced efficiency and monitoring of the injection molding process.
Conclusion
The significance of plastics injection molding in the manufacturing sector cannot be overstated. It is a process that fosters innovation and efficiency across various industries. With firms like Deep Mould at the forefront of this field, the potential for high-quality production and advancement is vast. As industries continue to demand precision and cost-efficiency, understanding these manufacturing processes will be key to future successes in product development and design.