Understanding the Importance of Plastic Mold Makers in Modern Manufacturing
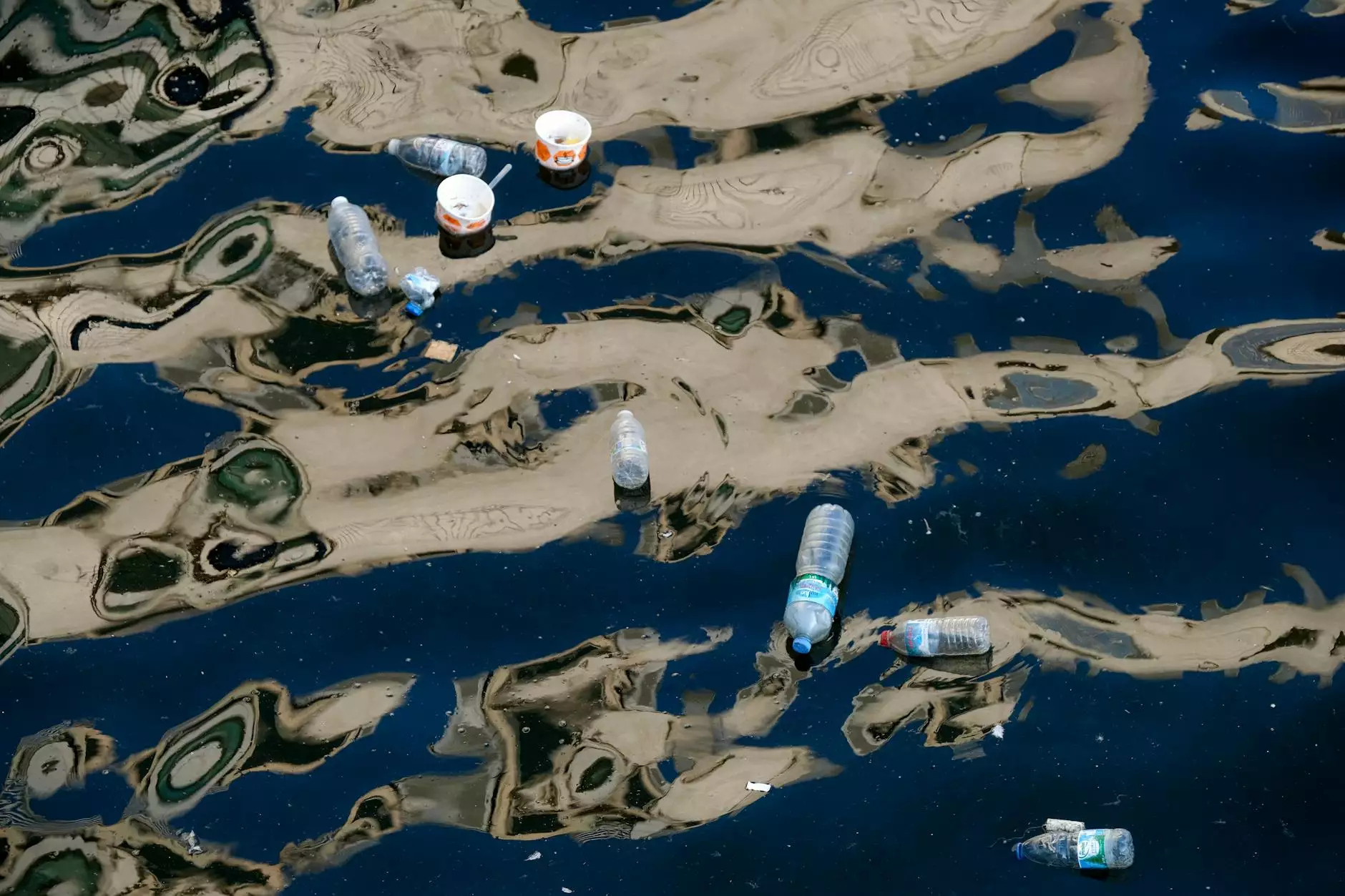
In today's dynamic manufacturing landscape, the role of plastic mold makers cannot be overstated. These skilled professionals are at the forefront of producing high-quality plastic products that reach consumers in various industries. From automotive components to household items, the expertise of mold makers is critical in ensuring precision, efficiency, and innovation in production. In this comprehensive article, we will explore the significance of plastic mold makers, their processes, and how they contribute to the manufacturing ecosystem.
The Role of Plastic Mold Makers in Manufacturing
Plastic mold makers are specialized craftsmen who design, create, and maintain molds used in the injection molding process. The injection molding technique is a popular manufacturing method for producing large volumes of plastic parts with high precision. Since the quality of the molds directly affects the quality of the final product, skilled mold makers are essential to the production chain.
Key Responsibilities of Plastic Mold Makers
- Designing Molds: Mold makers utilize CAD software to create intricate designs, tailoring molds to meet the specific needs of various products.
- Fabricating Molds: Using high-grade materials, mold makers build molds that can endure the pressures of injection molding while maintaining dimensional accuracy.
- Testing and Modifying Molds: After initial production, molds are tested to ensure they meet quality standards. Any necessary modifications are made to enhance performance.
- Maintenance: Regular maintenance and repairs of molds are crucial to prolonging their life and efficiency in production.
Importance of Precision in Mold Making
The success of any manufacturing process heavily relies on the precision of the molds used. Molds must be designed with meticulous attention to detail to ensure that parts fit together seamlessly during assembly. Any discrepancies can lead to a cascade of production issues, including increased costs and prolonged timelines.
Techniques for Achieving Precision
Modern plastic mold makers employ several techniques to achieve high precision in mold production:
- CNC Machining: Computer Numerical Control (CNC) machines offer unparalleled accuracy in cutting and shaping mold components.
- EDM Machining: Electrical Discharge Machining (EDM) is used for creating complex shapes that are difficult to achieve using traditional machining methods.
- 3D Printing: Many mold makers are now integrating 3D printing technologies to rapidly prototype molds before finalizing the designs.
Benefits of Working with Professional Plastic Mold Makers
Choosing a professional plastic mold maker offers several advantages for manufacturing companies:
1. Enhanced Quality Control
Professional mold makers implement strict quality control measures throughout the production process. This ensures that every mold produced meets the highest industry standards, resulting in superior quality products that satisfy customer demands.
2. Cost Efficiency
Investing in high-quality molds may seem costly upfront, but in the long run, professional mold makers can help businesses save substantial amounts of money. Quality molds lead to fewer defects, reduced material waste, and lower production costs.
3. Innovation and Customization
Every product has unique requirements. Professional plastic mold makers have the expertise to create customized molds that meet specific design and functional needs. This flexibility fosters innovation, allowing businesses to stand out in competitive markets.
4. Faster Turnaround Times
Experienced mold makers utilize state-of-the-art technologies and methodologies that streamline the production process. This efficiency translates to faster delivery of products to market, giving businesses a competitive edge.