Understanding the Role of a **China Lathe Machining Parts Factory** in Modern Manufacturing
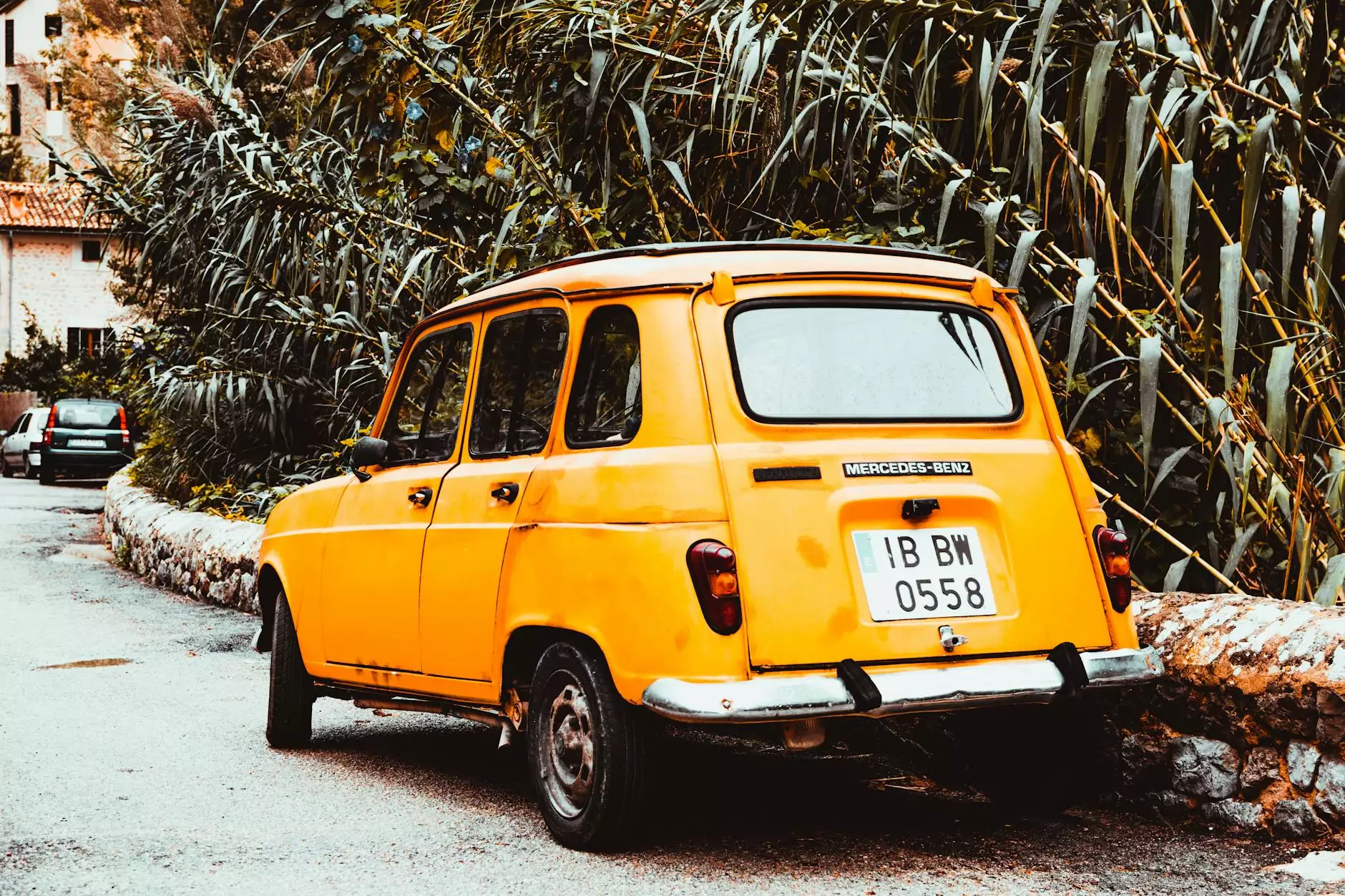
The global manufacturing landscape has evolved remarkably over the last few decades, with the China lathe machining parts factory playing a pivotal role in this transformation. Companies seeking precision and efficiency often turn to trusted manufacturers capable of delivering high-quality parts that meet stringent industry standards. This article delves into the significant advantages and capabilities of China lathe machining parts factories, highlighting how they can enhance your production processes.
What is Lathe Machining?
Lathe machining is a subtractive manufacturing process where a workpiece is rotated against a cutting tool to remove material. This method is fundamental for crafting cylindrical shapes, threads, and complex geometries. The precision and accuracy achieved through lathe machining make it an indispensable part of the manufacturing sector. Through intricate design and fast production times, lathe machining supports various industries, including automotive, aerospace, and electronics.
Types of Lathe Machining Techniques
- Turning: The primary operation in lathe machining, where material is removed to shape the workpiece.
- Facing: A process used to create a flat surface at the end of a workpiece.
- Threading: This technique is used to create helical grooves on a workpiece, essential for screws and bolts.
- Boring: Enlarging existing holes to precise diameters for perfect fits and alignments.
- Grooving: Cutting a groove into the workpiece for aesthetic or functional purposes.
The Advantages of Sourcing from a China Lathe Machining Parts Factory
Choosing to partner with a China lathe machining parts factory offers a plethora of benefits. Understanding these advantages can help businesses make informed decisions to enhance their manufacturing capabilities.
1. Cost-Effective Solutions
One of the most compelling reasons to source from a China lathe machining parts factory is the reduced production cost. Chinese manufacturers often benefit from lower labor costs and economies of scale, allowing them to offer competitive pricing without compromising on quality. Companies can significantly reduce their operating expenses while maintaining high production standards.
2. High-Quality Standards
Contrary to old stereotypes, modern Chinese manufacturing emphasizes quality. Many lathe machining parts factories in China adhere to international quality standards like ISO 9001, ensuring that every part produced meets rigorous testing and quality assurance processes. This commitment to quality translates into reliable products that enhance performance and longevity.
3. Advanced Technology and Machinery
China's commitment to adopting advanced manufacturing technologies is evident in its lathe machining parts factories. These facilities often utilize state-of-the-art CNC (Computer Numerical Control) machines, which provide enhanced precision and versatility. With high-tech equipment, manufacturers can produce complex parts with closer tolerances than ever before, increasing the overall quality of the products.
4. Expertise and Skilled Labor
Chinese factories boast teams of skilled engineers and technicians who are experts in their respective fields. With a focus on continuous training and development, these professionals stay updated on the latest innovations in machining. Their expertise is crucial in optimizing designs for manufacturability and ensuring effective communication throughout the production process.
5. Quick Turnaround Times
In a competitive market, speed is often as crucial as quality. The China lathe machining parts factory is known for its ability to deliver orders in a timely manner, regardless of size. The integration of lean manufacturing principles and efficient workflows ensures that projects move swiftly from conception to completion, allowing businesses to meet tight deadlines and respond to market demands rapidly.
What to Look for When Choosing a China Lathe Machining Parts Factory
With numerous options available, selecting the right lathe machining parts factory in China is paramount. Here are key aspects to consider:
1. Certification and Compliance
Ensure that the factory complies with international quality and safety standards. Certifications such as ISO 9001 or TS16949 demonstrate a manufacturer’s commitment to maintaining excellent quality in production processes.
2. Experience and Reputation
Look for manufacturers with a long-standing history of successful operations in the industry. Researching customer testimonials, case studies, and previous projects can provide insight into their performance and reliability.
3. Technology and Equipment
Examine the types of machinery and technology used in the factory. Advanced CNC machines and updated production techniques indicate a company’s dedication to quality and efficiency.
4. Customization Capabilities
Assess the factory’s ability to handle custom orders. A good lathe machining parts factory should be able to adapt to unique specifications and provide tailored solutions that meet your specific needs.
5. Communication and Support
Effective communication is vital for successful partnerships. Choose a factory that provides clear points of contact and support throughout the production process, ensuring any questions or concerns can be addressed promptly.
Conclusion: Unlocking Manufacturing Potential with a China Lathe Machining Parts Factory
Choosing to partner with a China lathe machining parts factory can unlock new levels of efficiency and quality for your manufacturing operations. By leveraging the benefits of cost-effectiveness, advanced technology, and a skilled labor force, companies can not only reduce production costs but also enhance their product offerings. As industries across the globe continue to evolve, finding the right manufacturing partner will be critical to maintaining a competitive edge.
If you are interested in exploring high-quality lathe machining parts and discovering exceptional solutions tailored to your needs, visit DeepMould.net today. Embrace the future of manufacturing with unparalleled precision, efficiency, and innovation.